Our solvent recovery system at the Ibaraki Plant won the Excellence Award at the 48th Environmental Award.
Teraoka Seisakusho Co., Ltd. (hereinafter referred to as "TERAOKA") has received the Excellence Awards at the 48th Environmental Awards (sponsored by the National Institute for Environmental Studies and the Nikkan Kogyo Shimbun, supported by the Ministry of the Environment)*1 for the "Closed VOC Collection System (hereinafter referred to as "this System")," volatile organic solvent recovery system installed at the Ibaraki Plant, jointly with Takasago Thermal Engineering Co., Ltd. hereinafter referred to as "Takasago Thermal Engineering").
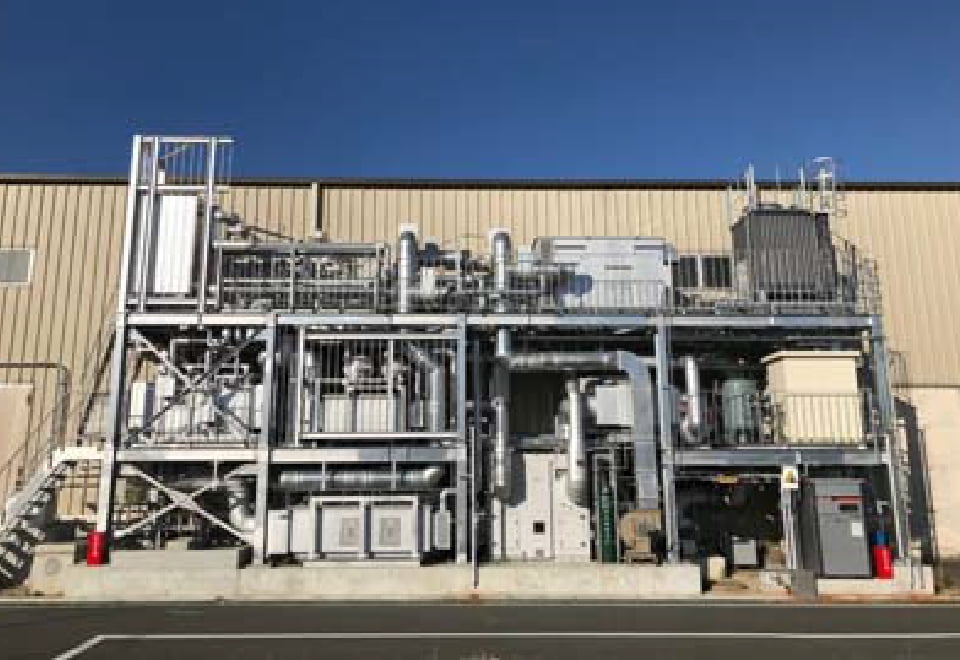
Background
In the manufacturing processes of adhesive tape plants and printing plants, there are dryers (solvent drying furnaces) that apply adhesive to film, paper and other materials, to dry them, and evaporate unnecessary solvents. The VOCs emitted there are known to cause photochemical smog and other health hazards to the respiratory system and mucous membranes. In fiscal 2018, 640,000 tons of VOCs were emitted in Japan, with approximately 50,000 tons emitted adhesive tape plants and printing plants (*2).
The conventional VOC treatment method, the one-pass system (Figure 1, left), treats exhaust gas containing VOCs emitted from dryers by combustion (*3) or adsorption recovery (*4). Although it complies with laws and regulations, it does not completely treat VOCs, and they are constantly released into the atmosphere at a certain concentration (tens to hundreds of ppm). In addition, the combustion method generates a large amount of CO2, so from the perspective of achieving a decarbonized society, non-combustion treatment of VOCs is desirable.
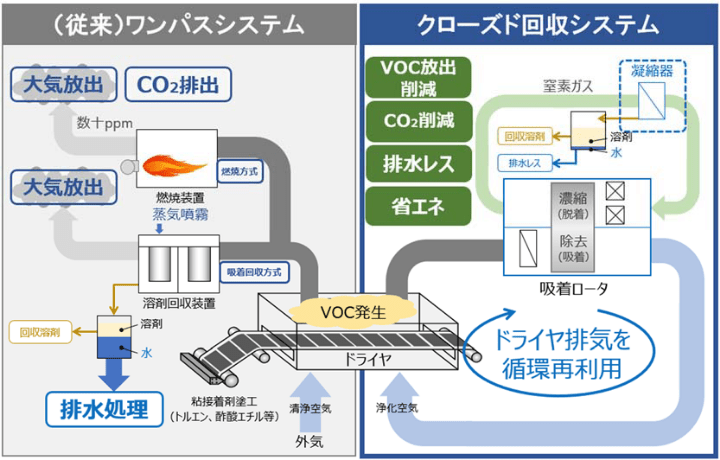
About this System
The System (Figure 1, right) purifies exhaust gas containing VOCs discharged from a dryer using an adsorption rotor, and then recycles and reuse it as air supply for the dryer. The main equipment consists of an adsorption rotor (using nonflammable zeolite as adsorbent), a brine chiller, a cooling tower, a compressor, etc., and has the following features
1. Significantly reduces the amount of VOCs released into the atmosphere by recycling and reusing (closed loop VOC recovery system) the exhaust air from the dryer as intake air.
2. Because this System is a non-combustion method, CO2 emissions from VOCs combustion processing are reduced.
3. Conventional adsorption recovery systems require wastewater treatment due to the use of steam, but this system recovers only the water in the circulation system, thus reducing wastewater (no wastewater)and wastewater treatment costs.
4. The closed system reduces the heating energy required to supply air to the dryer, especially in winter (energy saving).
This is the first closed system demonstration operation in Japan for an adhesive tape plant.
In March last year, TERAOKA installed this System at our Ibaraki Plant, and since June of the same year, we have been conducting demonstration operations, including 12-hour continuous operation, in collaboration with Takasago Thermal Engineering under the following design conditions of processed gas volume: 5,000 Nm³/h, processed gas concentration: 2,900 ppm and processed gas temperature: 70°C
This is the first attempt in Japan to demonstrate a closed system in an operating facility. Through the six-month demonstration operation until last December, we evaluated the quality of this System, the stability of the manufacturing environment, the characteristics of the recovered solvents, the effect of reducing VOCs emissions and the effect of reducing CO2 emissions, and confirmed the following results.
1. VOC atmospheric emissions were reduced by 95% compared to the one-pass combustion system.
2. CO2 emissions were reduced by 78% compared to the one-pass combustion system.
3. Product quality is equivalent to that of the one-pass combustion system.
4. The manufacturing environment is stable and low humidity, while the one-pass combustion system has humidity changes due to the supply of outside air to the dryer.
5. The recovered solvent is of high quality with a toluene purity of 99.9% or higher.
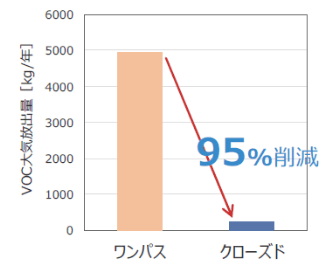
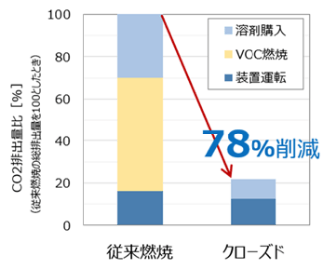
Received “Excellence Award” at the 48th Environmental Award
This initiative won the “Excellence Award” jointly with Takasago Thermal Engineering at the 48th “Environmental Awards” (sponsored by the National Institute for Environmental Studies and the Nikkan Kogyo Shimbun, supported by the Ministry of the Environment) *1. It was recognized as a technology that contributes to environmental conservation and the improvement of environmental quality.
Established in 1974, this award has been recognized as technological development, research, and performance activities that contribute to environmental conservation and the improvement of environmental quality. It is highly regarded by society as an award that combines history and credibility in the environmental field. There are four types of awards: “Minister of the Environment Award”, “Excellence Award”, “Superior Award” and “Judging Committee’s Special Award”.
A method of oxidizing and decomposing the carbon in VOCs by burning exhaust gas.
A method to recover VOCs by adsorbing them in exhaust gas on an adsorbent (activated carbon, etc.).